Yongxiang Polysilicon’s Circular Economy
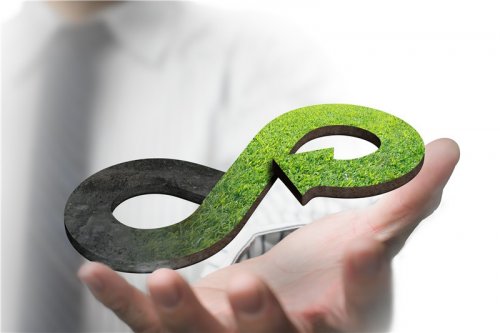
By CEIBS Professor of Finance and Accounting Oliver Rui and Xie Chun, Research Fellow at CEIBS Centre for Case Studies
Climate change and environmental pollution have consistently been topics of discussion since the beginning of this century. From a worldwide perspective, signs of global warming are becoming increasingly evident and extreme weather more frequent. In China, haze has been a public nuisance for many individuals. All these issues are inextricably linked to the global energy structure, one that is dominated by fossil energy. Seeking new sources of global energy has become vital.
Solar energy has shown great potential as it is both clean and renewable, and solar power is one of the most common paths towards solar energy utilisation. According to the principles of solar power generation, there are two main methods: photovoltaic and solar. Of the two, photovoltaic power generation accounts for more than 99% of installed capacity in China’s solar power generation industry, and more than 90% around the world. It is the most widely used method.
However, behind the rapid development of the industry, there are also large amounts of waste slag and sewage emissions – the result of the pursuit of short-term profit. What was originally intended as an environmentally friendly development measure has had the opposite effect. Blind expansion also leads to many potential dangers, such as overcapacity, therefore profits are declining across the entire industry.
Yongxiang Polysilicon has stuck to a principle of recyclability and green development from its inception, even in the face of huge temptation to earn a quick profit. Today, technological reform, energy conservation, and consumption reduction are not just a way for polysilicon manufacturers to show that they are socially responsible; it is also the only way for them to survive. The last seven years, which have been challenging for the entire industry, have also given Yongxiang Polysilicon an opportunity to fulfil its social responsibility.
Waste becomes treasure
Yongxiang Co Ltd, formerly known as Leshan Yongxiang Resin Co Ltd, was established in November 2002 by Sichuan Juxing Group. Since 2004, it has cooperated with Tongwei Group in the production of polysilicon; it has also established Leshan Yongxiang Silicon Industry Co Ltd and Sichuan Yongxiang Polysilicon Co Ltd. On November 15, 2007, a contract was signed by Tongwei Group, Sichuan Giastar Group and China Chengda Engineering Co Ltd for the design of a project with an annual output of 9,000 tonnes of polysilicon; the project was executed by Yongxiang Stock Co Ltd. Since then, Yongxiang Polysilicon has embarked on its own path.
It is a win-win situation. Yongxiang Polysilicon owes its success to Tongwei’s strategic investment and the close cooperation between the two companies. Liu Hanyuan, chairman of Tongwei Group, also extended his business into the green energy industry in which he has greatest interest – agriculture and fodder – as it is related to his other business interests. If we look at the history of Yongxiang Polysilicon’s development, we may find that every step it has taken was in line with its strategic approach to green energy.
Liu Hanyuan believes that to be socially responsible a company should, in addition to creating economic value for society, invent a model of long-term sustainable development within the context of environmental protection. If environmental protection could be taken into account in our initial efforts at economic development, that is a better approach than attempting to repair and improve the environment after it has been ruined. The field of polysilicon production, developing new energy, and strengthening technological reforms to achieve recyclable production is the implementation of this concept.
In December 2005, Yongxiang’s second-phase PVC project was completed and put into production, with a yearly production capacity of 100,000 tonnes. With the rapid expansion of PVC production by using the calcium carbide process, carbide slag, a by-product and solid waste, was also accumulated. In the past, the usual treatment methods for calcium carbide slag was either to have companies near the seaside use the waste for land reclamation, or companies in mountainous areas would dispose of it directly in the valley. Later, according to national regulations for hazardous waste management, calcium carbide slag could no longer be directly used as landfill. This posed a major challenge for the company.
Liu Hanyuan believes that anything categorised as ‘waste’ is merely something that has not been fully utilised; for example calcium carbide slag must have some other use which people have simply failed to grasp. He therefore asked Feng Dezhi, chairman of Sichuan Yongxiang Co Ltd, to set up a special R&D task force to study the value to be obtained from using calcium carbide slag. In accordance with the concept of the circular economy industry chain, Yongxiang’s technical staff made a breakthrough which is the first in China. Through the dry acetylene process while producing PVC, after proper drying the waste carbide slag produced can be used to produce cement.
At that time, the water content of calcium carbide slag produced by Yongxiang’s wet acetylene was 35-40%; unless they could reduce it to 10-13%, it could not be used to produce cement. From December 2007 to May 2009, Yongxiang invested RMB69 million to eliminate the existing hydrometallurgical process and adopted dry acetylene production technology. The calcium carbide slag produced from this method could be directly used for cement production.
So far, the first main cycle in Yongxiang’s circular economy (chlorine-alkali-PVC-carbohydrate slag cement industry chain) has been completed. Chlorine and hydrogen, which are by-products of chlorine-alkali, are raw materials for PVC; meanwhile calcium carbide slag, by-product of PVC, is the raw material for cement.
On October 18, 2008, even as the dry acetylene process was eroding the popularity of calcium carbide wet hydrolysis, a calcium carbide slag cement project into which Yongxiang invested more than RMB300 million was also completed and put into production. It has an annual production capacity of 1 million tonnes of cement, thus completely resolving the old bottleneck that restricted the company’s development.
Technical reform
Feng Dezhi and his team did not rest on their laurels after the success of the cement project because, as they saw it, there was still work to do in perfecting the industrial chain of the circular economy. In addition, soon after the first phase of the Yongxiang polysilicon project was put into production, a ‘hard winter’ swept across the entire industry: the price of Polysilicon began to fall. For seven years, the price kept falling, first from RMB3.5 million per tonne to RMB1.8 million per tonne, and then to RMB700,000, to RMB300,000, and it finally stopped at RMB10,000. The entire polysilicon industry was struggling. At that time, there were more than 80 polysilicon manufacturing companies in the country, most of them fell from the peak to the valley. Yongxiang’s suffering was even worse: it had never even reached a peak, it was barely born when the ‘winter’ came, and so it struggled badly.
There was fierce competition, there was a downward trend in profits within the overall polysilicon industry. At the same time, China’s polysilicon industry had gradually become an oligopoly: the leading position belonged to GCL POLY, closely followed by DAQO New Energy, TBEA, and Renesola Co Ltd; while Sinosico, LDK Solar, and Yongxiang resumed production after technical reform was completed. Although polysilicon prices rose in 2015, improving companies’ profitability, most of the orders were still in the hands of several large enterprises.
Yongxiang did not give in. They were convinced that their principled stance on recyclable development would ultimately be a way to overcome the challenges being faced. However technological innovation requires huge capital and manpower. For a company with annual production capacity of more than 10,000 tonnes of polysilicon, their resolve was substantial. “Especially from the end of 2013, on the basis of the first three technical transformations, we resolutely invested over RMB600 million in the transformation of the Yongxiang Method with cold-hydrogenation technology to realise the comprehensive utilisation of waste recycling. We reduced the production cost from RMB160,000 per tonne to less than 80,000 per tonne, a decrease of over 50%. This saved 250 million kwh of electricity yearly, equivalent to approximately 30,700 tons of standard coal,” Feng Dezhi said with pride.
Achieving a circular economy
After four technical reforms, a complete circular economy industrial chain was realised. The completion of the comprehensive use of calcium carbide slag cement project has made good use of calcium carbide slag, in addition to lowering the overall cost of production; the cement and building materials produced can be used in Yongxiang’s plant construction and other projects.
At the same time, the calcium carbide slag cement plant can also consume a part of the acidic water produced by chemical reaction trace substances in Yongxiang’s chemical circular economy industrial chain. Acidic water needs to be neutralised with alkaline substances, and calcium carbide slag is an alkaline. After neutralisation is completed, the chlorine can be filtered out, and the remaining residue can enter the cement plant again. In order to survive the industry’s hard winter, Feng Dezhi continuously encouraged Yongxiang’s R&D team to solve more problems, thus perfecting the company’s circular economy industry.
The basic chemical resources for the production of polysilicon — the brine mines that can produce hydrogen and chlorine — are Yongxiang’s unique natural resources, and the hydrogen and chlorine gas produced by the electrolytic cell decomposition have their own characteristics: hydrogen can be drained or purified before being put into use again, but chlorine is a highly toxic gas and cannot be easily discharged. After research, Yongxiang decided to turn chlorine into hydrogen chloride, and then let the colourless, transparent solution – hydrogen chloride – react with silicon powder to form a raw material for the production of polysilicon: trichlorosilane. Then, chlorine is replaced by reduction and only silicon remains. In order to obtain high-purity silicon, repeated distillation, purification, and reduction must be performed before a 99.9999999% pure polysilicon product can be obtained.
This is how the second main cycle of Yongxiang’s circular economy was formed: the chlorine-alkali-hydrochlorosilicone-polysilicon industrial chain. On one hand, it helps to reduce the company’s costs for raw material procurement, transportation and those related to product sales, improving its overall efficiency. On the other hand, a closed loop of materials can help reduce emissions and protect the environment.
Yongxiang Polysilicon has undergone three rounds of technological transformation and upgrading in the short span of eight years. Through this, the company gradually gained ground despite the hardships of the industry, and survived. However, the company’s achievements do not prevent it from further pursuing energy conservation and ways to reduce consumption. At the end of 2013, based on the first three rounds of technical transformation, Yongxiang resolutely invested more than RMB600 million and used the Yongxiang Method to combine cold-hydrogenation technology transformation to achieve comprehensive utilisation of waste recycling; the fourth technical transformation was completed.
Spring has come
At the 2014 Beijing APEC meeting, China and the United States issued a joint statement on climate change. China proposed that its carbon dioxide emissions should reach its peak by roughly 2030 and said it plans to achieve a non-fossil energy share of about 20% of primary energy consumption in the same year. This indicates that cleanliness and renewability have become the trend of energy development in the future, and solar energy is a clean and renewable energy. However from a global perspective, fossil, coal, and natural gas were still among the top three primary resources in the global energy structure between 2013 and 2014.
China’s non-fossil energy consumption accounts for only 9.8% of primary energy consumption. Therefore, in order to achieve the goals proposed by China, the country must vigorously develop solar energy, wind power and other renewable energy resources in the future. In terms of the use of solar energy, at present, China’s solar power is at less than 0.03% of development. Considering the country’s size and the fact that it has the world’s second largest reserve of solar energy resources, there is huge room for future development.
Now, Yongxiang Polysilicon has amassed an industrial scale of 15,000 tonnes of polysilicon, 120,000 tonnes of PVC, 100,000 tonnes of caustic soda, 40,000 tonnes of trichlorosilane, and 1 million tonnes of calcium carbide slag cement. At the same time, Yongxiang Polysilicon has carried out a large number of independent innovations and technical transformations in the areas of resource recycling, closed materials running, and recycling of by-products, forming a complete circular economy industry chain. It has successfully earned a spot among the top three polysilicon production enterprises in the country, and the biggest in Southwestern China. However, this is not the end of Yongxiang’s efforts. Convinced that their achievements are derived from technological innovation, and guided by a strategy that takes into consideration both profits and social responsibility, Yongxiang will surely add more green to the world in the future. As Feng Dezhi smiled and said when the fourth round of reform was successful, “Now spring is in the air.”
This article is based on the CEIBS case #CI-715-066 “The Key to the Success of Yongxiang polysilicon - circular economy industrial chain”.